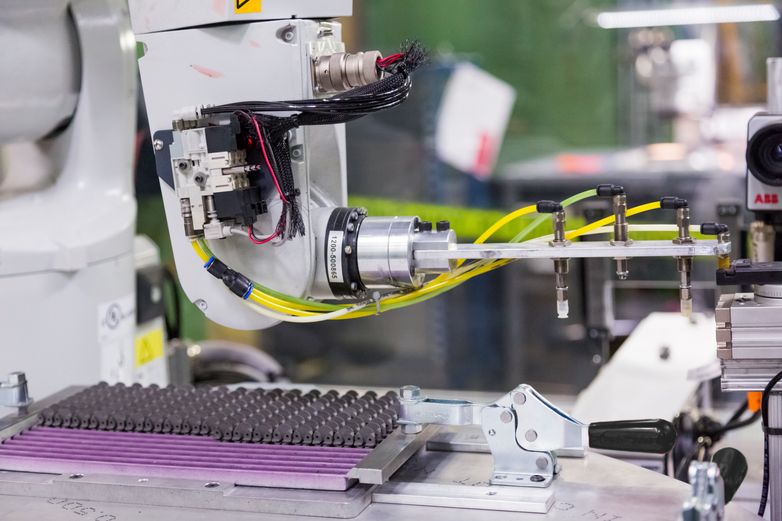
MIM Series Part 4: Molding
MIM Series Part 4: Molding
Molding, the fourth part of this blog series on MIM, focuses on loading compounding pellets into a MIM machine to produce a "green part". This part is about 20% larger than the final part, but has the same geometry. The percentage is based on the type of metal used, which is known before mold completion. This allows for the tool to be created correctly, so the final part meets exact specifications.
For more information about the MIM process, contact OptiMIM engineers today!
When pelletized feedstock is fed into either standard or multi-slide MIM machines, it is heated and injected into a mold cavity. This high-pressure injection creates the "green" part. The part cools quickly and is ejected from the mold. Only the binders melt in the molding phase, and tooling can have multiple cavities for higher production rates. 70% of MIM defects result from tooling and another 15% from molding, making these steps critical to a correct, defect-free final part.
Molding Machines (H3)
The metal powder is mixed with plastic and paraffin binders at a ratio of approximately 40% binder and 60% metal. This percentage can vary based on the powder size and desired tool shrinkage. MIM parts can shrink from their original molded condition (known as the green state) to a finished sintering condition by 16-21%. This ratio is known as powder loading. There are two common methods for mixing MIM materials: using a planetary mixer or a tubular mixer. These mixers blend the material, which can be done at room temperature or heated. When heated, the material is mixed to a temperature that causes the binders to melt. Mixing continues until the metal powder is uniformly coated with the binders. The mass is then cooled and pelletized. Both mixing processes are batch processes, ensuring the metal powder is uniformly coated with the binders. The resulting pelletized mix, known as feedstock, is then ready for the molding machine.
The planetary mixer uses a batch process and is slower. It produces inconsistent blends and introduces more variables than other available mixers. The tubular mixer, which is also a batch process, is the preferred method used by OptiMIM. It offers faster throughput and creates consistent blends with fewer variables.
Compounding
OptiMIM utilizes conventional MIM machines that have a typical cycle time of about two shots per minute. It is ideal for larger parts and for parts that have multi-cavities and are also high-volume production. Conventional MIM machines require complex tooling, long runner systems, and long material residence time in the machine and mold. Some of the tools for conventional MIM machines could have shorter lives depending on the complexity of the part.
In part five of this series, you'll learn how the part goes from "green" to "brown". The next blog will focus on the debinding portion of the MIM process.